导压比 3:1, 负载作用, 负载控制阀
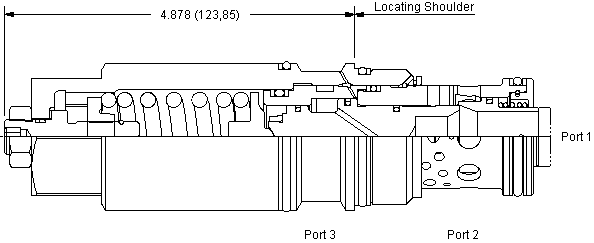
带先导协助开启的负载反作用,负载控制阀结合了两种阀的功能;单向阀与溢流阀。它允许油液从方向阀(口2)到负载口(口1)单向自由流通,同时直动式,先导协助溢流阀功能可以控制从口1到口2的液流。口3的先导协助以先导比率的作用系数降低了溢流功能的有效设定值。
- 负载反应负载控制阀的设定值都为最大负载压力值的1.3倍。
- H范围的最大推荐负载压力为3080 psi (212 bar)。
- J范围的最大推荐负载压力为3850 psi (265 bar)。
- 顺时针旋转降低设定值,减小负载。
- 对于H系列,完全泄压设置值为1000psi(70bar);对于J系列来说,最小为2000psi。
- 2口的背压将直接叠加到有效溢流压力上,此时压力值为(1+先导比)×背压。
- 此阀功能上是3口平衡阀。阀座形式是锥阀结构,动作调节过程又是滑阀结构,所以其集结了两种结构的优点。
- 这类阀与锥阀芯的结构相比,可以调节更为广泛的流量。对于这种长距离的冲击动作,这里设计了单向的阻尼结构,令其开启更平稳,关闭更迅速。
- 耐腐蚀插装阀适用于在腐蚀性环境中使用,并通过型号代码后缀/AP标识外部不锈钢组件,或/LH标识外部镀锌镍镀组件。有关选项,请参阅配置部分。欲了解更多详情,请查看位于技术资料下的结构材料页面。
- 所有的3口平衡阀,负载控制阀,以及先导开启单向阀都结构上可以相互替换。(对同样的规格情况下,他们是相同流量路径相同孔型)。
- Sun负载控制阀和平衡阀都可以之间安装于执行器外壳处,一次给执行器、回路更安全的保护。
- 此阀在所有口之间完全密封。
- 这款阀有完全的溢流能力。
- Sun浮动式的结构可以最大限度地减少由于过大的安装扭矩以及孔型加工的误差所造成的干涉现象。
插孔 | T-19A |
系列 | 4 |
通流能力 | 120 gpm480 L/min. |
最大操作压力 | 5000 psi350 bar |
先导比 | 3:13:1 |
最大推荐负载压力 | See Technical FeaturesSee Technical Features |
工厂默认的设定值 | 2 in³/min.30 cc/min. |
回座时最大泄漏 | 5 drops/min.0,3 cc/min. |
单向开启压力 | 25 psi1,7 bar |
调节 - 从最小设定到最大设定的逆时针圈数 | 77 |
复位 | ≥77% of setting≥77% of setting |
阀头部安装六角尺寸 | 1 5/8 in.41,3 mm |
阀安装扭矩 | 350 - 375 lbf ft474 - 508 Nm |
调节螺栓的内六角尺寸 | 7/32 in.5,5 mm |
锁紧螺母六角尺寸 | 3/4 in.19,1 mm |
锁紧螺母力矩 | 25 - 30 lbf ft35 - 40 Nm |
Seal kit - Cartridge | Buna: 990019007 |
Seal kit - Cartridge | Polyurethane: 990019002 |
Seal kit - Cartridge | Viton: 990019006 |
Hysteresis is the difference between the pressure at which the valve will crack open and then reseat closed. Sun's counterbalance valve's hysteresis is typically less than 15%, which means the valve will have reseated to a closed position at 85% of its cracking or opening pressure.
It is always recommended that a counterbalance valve be set before it is installed in an application. Correctly setting a counterbalance when it is installed is very difficult due to the pilot assist and the interaction with the actuator. Once installed the adjust screw should be considered a manual override.
A closed loop transmission is meant to transfer the energy from dynamic braking to the prime mover. A counterbalance valve would put the energy in the form of heat into the small amount of oil contained in the loop. Backpressure caused by dynamic braking from the pump and charge pressure complicate matters. "Putting a vented counterbalance in a closed loop transmission is a crime; putting a non-vented valve in is a felony; putting a 10:1 valve in is a capital offence." Jeff Baker
First the valve is set to just crack open at the desired setting. The pressure is dropped to zero and then brought up to 85% of the setting. The valve is then piloted open and allowed to reseat. At this point the leakage rate must be less than 5 drops per minute. One detail that makes this test critical is extremely clean oil. If a valve leaks in an application, the seat has probably been damaged by contamination and the valve should be replaced. Before removing any valve, ensure machines and loads are mechanically held in position and that the valve is not under pressure at the time of its removal.
Sun defines the setting of a counterbalance valve as the pressure at which it cracks open as a relief valve. The flow rate at "crack" is the point where drops turn to a stream, about 1-2 cubic inches per minute. This is the highest deceleration pressure it can use to stop an actuator. The valve should be set at least 1.3 times the maximum expected load-induced pressure at port 1. In many cases the maximum load-induced pressure will be the same as the system relief setting.
Three-port vented, or atmospherically referenced, counterbalance valves are considered problem solvers for existing circuits that used a three port, non-vented valve. If a vented valve is required in a new design, four-port valves are recommended. Atmospherically referenced valves, over time, will leak externally or allow moisture into the spring chamber (resulting in corrosion) even though the spring chamber is sealed.
Generally, the 25 psi check spring is recommended for most applications as it is more robust and insensitive to rapid flow reversals. The 4 psi check cracking pressure should be used if there is a need to pull in make-up oil.
We do not recommend it. There is a possibility that the pilot area could get filled with oil and slow down or prevent the closing of the valve. A correct solution is to connect port 3, the pilot port, to port 2, the inlet port.
Backpressure at port 2 (inlet) may adversely effect the operation of a three port counterbalance valve as it directly opposes pilot pressure. When backpressure exceeds pilot pressure, it adds to the setting of the valve at a rate of 1 plus the pilot ratio times the backpressure, i.e. with 200 psi (14bar) back pressure at port 2 on a 3:1 counterbalance valve, the setting would increase by 800 psi (55 bar). In effect, backpressure drives the counterbalance valve closed. Using vented counterbalance valves typically will correct this problem.
The vast majority of counterbalance applications are satisfied with a 3:1 pilot ratio. Lower pilot ratios will increase system stability and higher ratios will be more efficient. 10:1 pilot ratio valves generally should be avoided.
There are 2 styles of load-reactive counterbalance cartridge valves. The first was designed by Racine and has the pilot in port 1 or the nose of the cartridge. The second style that Sun adapted was conceived by Fluid Controls, and has the load port (port 1) at the nose and the pilot coming in port 3. Sun co-founder John Allen said that a counterbalance was a valve designed around a spring. For a given size of cartridge you design a spring that has the most force and rate that can be wound, and then design the rest of the valve. The spring force dictates the relief area needed to achieve a setting.
The Racine design has 2 diameters. There is a pilot diameter and a larger diameter that creates the annular relief area. In order to maintain capacity the larger diameter has to be as large as possible. In order to increase pressure settings the annular relief area needs to be reduced. Because the big diameter is fixed and the differential annular area is being reduced, the result is the pilot diameter increases; hence the high pilot ratios.
Sun's (Fluid Control's) design has 3 diameters, the small one and the middle one defining the relief area and the middle one and the large one defining the pilot area. This design gives us the freedom to create pilot ratios that fit the application.
No. The counterbalance will be less violent than the check valve but the flow dynamics create backpressure spikes that can damage the valve. The circuit needs to be designed to dissipate the energy in a controlled fashion.
Vented counterbalance valves should be used if you have backpressure in port 2 (inlet). Typical applications are regeneration circuits, master-slave circuits and servo/proportional valve circuits.
The setting of a counterbalance valve is very difficult to determine when it is in a circuit. This is due to cross-piloting, load-induced pressure, and cylinder ratio. The best way to check the setting is to remove the valve from the circuit. Before removing any valve, ensure machines and loads are mechanically held in position and that the valve is not under pressure at the time of its removal. Screw the valve into a simple, single cavity, line mounted body. Port 1 should be connected to a pressure source and ports 2 & 3 should be open. Increase the pressure on port 1 until the valve just starts to open. Repeat several times to ensure consistency.
The 5 drops/min. are at the point of reseat which is 85% of cracking pressure. If the valve is set correctly it will never see a load that is higher than 77% of cracking (1/1.3). At this pressure in a typical system the counterbalance can be considered a zero leak device. Using counterbalance valves to prevent drift is an accepted and common practice on almost all manlifts and hydraulically operated cranes. If a load drifts because of the counterbalance valve, the seat has probably been damaged and the valve should be replaced.
While cylinder drifting is often attributed to a leaking or damaged counterbalance valve, it can also be caused by cylinder seal leakage or changes in oil temperature. If you believe the seat of the counterbalance valve has been damaged, which can be caused by shock or contamination, it is advisable to replace the valve with a new factory set valve. Always follow the manufacturer's recommendations for servicing of hydraulically actuated machinery, and insure all loads are mechanically supported and cartridges are not under pressure when removed.
There are exactly 250 Sun drops in a cubic inch or 15 in a cc.
Yes it is sealed; however every time the valve is cycled a small amount of oil passes into the spring chamber--about 1 drop for every 4000 cycles. If the vent is blocked, the spring chamber will eventually fill with oil, building pressure until the valve won't open.
Counterbalance valves are pressure dependent devices, not flow dependent. They are designed to create pressure drop for their operation, so it is important not to oversize them. A higher pressure drop will generate greater system stiffness and help improve stability.
Two areas work to open a counterbalance valve, the relief area and the pilot area; the pilot area divided by the relief area equals the pilot ratio. Reverse flow from port 1 to port 2 is blocked by the check valve until a pilot pressure is sensed at port 3 (pilot) that is inversely proportional to the load pressure at port 1 (load). The pilot pressure at port 3 effectively reduces the relief valve setting. The setting is reduced according to the ratio of the differential pilot area on the piston compared to the differential relief area. For example, in a valve with a 3:1 pilot ratio, set for 3000 psi with a load of 2000 psi, the pilot pressure required to open the relief valve is 333 psi, i.e. (3000 psi - 2000 psi)/3 = 333 psi pilot pressure.
To calculate the pressure required to lower a load, use the following equations. These equations are under ideal conditions and do not consider any backpressure in the circuit or any effects of temperature on the oil.
- Sun Cartridges with EPDM Seals
- Sun采用负载匹配™技术以降低能耗
- 最新的QuickSelect负载保持阀快速选型工具
- 追求完美的平衡阀
- Counterbalance/Pilot-to-Open Cartridge Valve Technical Tips
- Another Optimized Solution from Sun Hydraulics!
- Sun FLeX™系列电磁阀&线圈
- QuickDesign with SmartConnect Offers Drag-and-Drop Schematic Tool
- Sun LoadMatch™ Valves Save Energy!
- Sun推出抗腐蚀产品解决方案
- Sun’s Cartridge Symbol Library
- 可变先导比 ( LoadAdaptive™ ) 平衡阀 (1.5 MB(兆))
- Choosing Counterbalance Valves
- Sun插装阀插孔 (551.8 KB)
- 负载控制及运动控制插装阀 平衡阀和先导液控单向阀 (668.64 KB)