Model: YCCKLHNAK
Amortiguar y bloquear ensamblaje con selector y anti-cavitación anti-retorno
Function
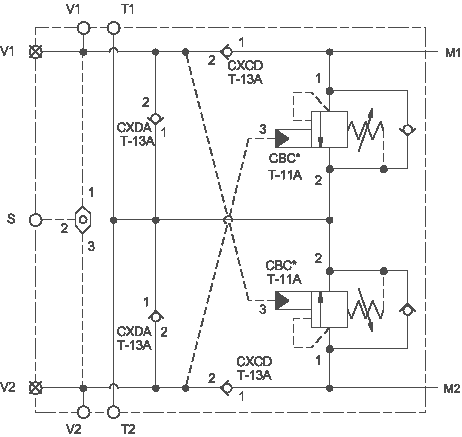
Port Designators [ + ]
Modifiers | Ports |
B, B/S | Port S: 1/4" NPTF; Ports V1 & V2: 3/8" NPTF; Ports T1 & T2: 1/2" NPTF; |
C, C/S | Port S: 1/4" NPTF; Ports V1 & V2: 1/2" NPTF; Ports T1 & T2: 1/2" NPTF; |
J, J/S | Port S: SAE 4; Ports V1 & V2: SAE 8; Ports T1 & T2: SAE 10; |
K, K/S | Port S: SAE 4; Ports V1 & V2: SAE 10; Ports T1 & T2: SAE 10; |
Technical Features [ + ]
This valve assembly provides overrunning load-control, load-port relief protection, supplies make-up oil, and flushes hot dirty oil out of the actuator and includes a load sense shuttle for brake release. All oil coming out of the actuator returns to tank through port T.
- The counterbalance valves should be set at 1.3 times the maximum load induced pressure.
- Low pilot ratio counterbalance valves (3:1 vrs 10:1) may be necessary to generate enough pressure to release a brake.
- Hydraulic motors leak. Therefore a mechanical brake is recommended to positively lock any stopped live load.
Technical Data [ + ]
Body Type | montaje directo a motoresmontaje directo a motores |
Interface | Eaton/Char-Lynn H & SEaton/Char-Lynn H & S |
Capacity | 15 gpm60 L/min. |
Mounting Hole Diameter | .34 in.8.6 mm |
Mounting Hole Depth | ThroughThrough |
Mounting Hole C'bore Diameter | .53 in.13,5 mm |
Mounting Hole C'bore Depth | .28 in.7,1 mm |
Mounting Hole Quantity | 44 |
FAQs [ + ]
There are exactly 250 Sun drops in a cubic inch or 15 in a cc.
Reasons to anodize:
- To increase corrosion resistance. Sun uses 6061-T651 aluminum. It is one of the most corrosion resistant aluminum alloys there is. Whether or not anodizing improves the corrosion resistance of 6061 aluminum is debatable. We have yet to have a manifold returned because of corrosion.
- Appearance (color). The 2 colors that would appeal to Sun would be blue or black. Unfortunately these are the colors that are hardest to do consistently.
- To provide a hard wear surface. Sun does not make parts-in-body valves. The manifold is just plumbing. We don't need a wear surface.
- Because everyone else does it. Bad reason.
Reasons to not anodize:
- Cost. It's another process.
- Logistics. When you make tens of thousands of manifolds a month and you anodize hundreds, it's a problem. Consistency. See above.
- Stamping. After a body is anodized you cannot do any more stamping without making a mess.
Inspection. Have you ever tried to look for burrs in a black anodized body? It's the old blackboard factory at night scenario. - Torque. You will experience an increase in breakaway torque when removing items from an anodized manifold.
- Fatigue life. This is the best reason to not anodize. Fatigue failure is a very complex phenomenon. What it takes to initiate a crack is difficult to predict. What it takes to propagate a crack is readily defined. Anodizing produces a very thin, very hard, and very brittle surface on aluminum. The first time you pressurize an anodized aluminum manifold you have initiated fatigue cracks. Whether or not the stress is enough to propagate the cracks is a matter of pressure and manifold geometry. Anodizing an aluminum manifold grossly reduces the fatigue life by anywhere from 20% to 50%.
Direct-acting valves are used to prevent over pressure, and pilot-operated valves are used to regulate pressure. If you are unsure, use a direct-acting valve. Sun's direct acting valves are very fast, dirt tolerant, stable, and robust. Sun's pilot-operated valves are moderately fast, they have a low pressure rise vs. flow curve, and they are easy to adjust.
Notes [ + ]
- All SAE o-ring porting per ISO 11926. All NPTF porting per ANSI B1.20.1. All BSPP porting parallel thread.
- For detailed information regarding the cartridges contained in this assembly, click on the models codes shown in the Included Components tab.
- Important: Carefully consider the maximum system pressure. The pressure rating of the manifold is dependent on the manifold material, with the port type/size a secondary consideration. Manifolds constructed of aluminum are not rated for pressures higher than 3000 psi (210 bar), regardless of the port type/size specified.
Additional Resources [ + ]
Realces
- Conjuntos integrados: Soluciones que hacen crecer su reputación
- Nuevas soluciones rápidas de avance y alimentación
- Putting Sun at the heart of hydraulic regenerative braking systems
- NUEVO: Soluciones de control de flujo con prioridad ajustable
Technical Tips
- Manufacturing Sun Cartridge Cavities (522.27 KB)
Technical Information
Included Components[ + ]