Electro-proportional 3-way flow control valve, meter in (740 Series)
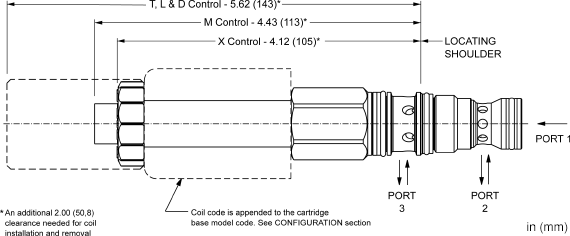
This valve is a 3-way, meter-in, electro-proportional throttle. The flow path, unenergized, has the supply blocked at port 1 and port 2 is drained to tank at port 3. Energizing the coil generates a closing force on the spool, creating a metering orifice in the 1 to 2 direction that is proportional to the coil command current. The valve self-compensates in the 1-to-2 direction and with the addition of an external compensator will provide pressure compensated flow control.
Flow in the 2-to-3 direction is not proportional and is limited in the interest of increased resolution and capacity. Flow capacity in the 2-to-3 direction is about 1.5 gpm (6 L/min). This valve is meant to be used in a circuit that has a separate passage to tank such as a cushion lock circuit. Two FMDFs in conjunction with a cushion lock circuit create a meter-in/meter-out 3-position 4-way.
- Note: Flow in the 2 to 3 direction is limited to about 1.5 gpm (5 L/pm).
- The transition between positions is closed.
- Using 2 3-ways to create a 4-way allows one to choose existing flow ranges instead of cutting a special spool.
- These valves may be pressure compensated by an external, modulating, logic element. Use LR_C-XHN for a bypass circuit or LP_C-XHN for a restrictive circuit.
- The valve provides a degree of self-compensation and may be used as a flow control. To increase the accuracy of flow control, an external, modulating, logic element can be used to maintain a constant flow over a wider range of flows and pressures. See performance curves for additional information.
- For optimum performance, an amplifier with current feedback and adjustable dither (100 - 250 Hz) should be used.
- Incorporates the Sun floating style construction to minimize the possibility of internal parts binding due to excessive installation torque and/or cavity/cartridge machining variations.
Cavity | T-11A |
Series | 1 |
Capacity | 9 gpm34 L/min. |
Maximum Operating Pressure | 5000 psi350 bar |
Maximum Valve Leakage at 110 SUS (24 cSt) | 2 in³/min.@1000 psi30 cc/min.@70 bar |
Manual Override Force Requirement | 5 lbs/1000 psi @ Port 133 N/100 bar @ Port 1 |
Manual Override Stroke | .10 in.2,5 mm |
Solenoid Tube Diameter | .63 in.16 mm |
Valve Hex Size | 7/8 in.22,2 mm |
Valve Installation Torque | 30 - 35 lbf ft41 - 47 Nm |
Hysteresis (with dither) | <4%<4% |
Hysteresis with DC input | <8%<8% |
Linearity (with dither) | <2%<2% |
Repeatability (with dither) | <2%<2% |
Recommended dither frequency | 140 Hz140 Hz |
All flow is blocked, hence the term priority. The priority flow has to be satisfied.
The valve acts as a 2 port restrictive flow control.
The spring force in our flow controls equates to about 100 psi (7 bar). This is high enough to give the valves acceptable capacity and not too high for proper circuit operation. 100 psi (7 bar) is the spring force; at the upper end of the flow control's range, the drop through the valve will be as high as 250 psi (17 bar) before it starts modulating.
There are exactly 250 Sun drops in a cubic inch or 15 in a cc.
In a meter-in flow control circuit if the pump is set at 3000 psi and the load is 2000 psi the drop through the flow control is 1000 psi. In a meter-out circuit with the load at 2000 psi the drop through the flow control is 2000 psi.
We claim +/- 10%. We set to +/- 5% in production testing to allow for differences in customers' conditions. If you want accuracy, stay in the bottom 2/3rds of the range. Our 12 gpm (45 L/min.) flow controls are quite flat at 9 gpm (34 L/min.) and dead flat below 6 gpm (23 L/min.), until you get to the bottom of the range. Below about .25 gpm (1 L/min.), spool leakage and orifice conditions start to limit accuracy.
I am afraid not. Unless you are overflowing your current valve and correctly size ours, you are not likely to notice any improvement. Priority flow controls are not efficient devices. They are an easy way to get more than 1 source of oil from 1 pump but they can generate a lot of heat. Try to size your actuators so the pressures are similar on both the priority and the bypass circuits. If you can't do that, try to have the lower flow leg be the lower pressure. The pump pressure is determined by whichever leg is higher and if there is flow that is taking a pressure drop that is not doing work it is creating heat.
- Please verify cartridge clearance requirements when choosing a Sun manifold. Different valve controls and coils require different clearances.
- An additional 2.00 inches (50,8 mm) beyond the valve extension is needed for coil installation and removal.
- QuickDesign with SmartConnect Offers Drag-and-Drop Schematic Tool
- Sun Offers Zinc-Nickel Plating for Corrosion Resistance
- Sun's New FLeX Series Solenoid Valves & Coils
- Sun Expands Corrosion-Resistant Solutions
- Sun Cartridges with EPDM Seals
- Our FLeX family of solenoid-operated valves is expanding
- Sun's Proportional Valves Enable Meter-in and Meter-out in Motion Control Circuits
- High Capacity Electro-Proportional Throttle Valve
- Factory-tuned, optimized electro-hydraulics right out of the box
- Electro-Proportional Basics Explained
- CavitySaver multi-function valves deliver single-cartridge solutions
- CANpoint XMD Configuration Software
- Check Valves, Flow Control and Priority Flow Control Valves Technical Tips
- Proportional Amplifiers and Ancillary Products (2.06 MB)
- Manufacturing Sun Cartridge Cavities (522.27 KB)
- Solenoid Coils for Switching and Proportional Valves (975.2 KB)
- Cavity Information (S-171) and Tooling
- Sun's Floating Style Screw-In Cartridge (1.06 MB)
- Sun Model Code Explanation; 999-901-334 (343.9 KB)
- Fluid Recommendations: Oil Viscosity, Cleanliness & Temperature
- Cartridges: Materials of Construction
- Units of Measure, Settings, and Conversions
- Electro-Hydraulic Terms and Definitions (2.94 MB)
- Performance Data
No coil selected.