Cetop 05: Réducteur de pression 3 voies sur A avec clapet de by-pass et orifice 4 externe
Function
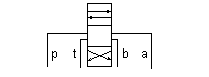
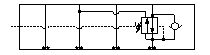
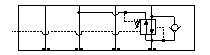
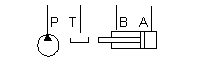
Modifiers | Ports |
NB2, /10, /11, /15, /16, /S, /S3, /V, /Y, /Y3 | External Port: SAE 6; |
NB2/1A, /1B, /1F, /1G, /M, /T, /T3, /W, /W3, /Z | External Port: 1/4" BSPP; |
Type de Corps | ModulaireModulaire |
Plan de Pose | Cetop 05Cetop 05 |
Caractéristiques du Corps | Réducteur de pression 3 voies sur A avec clapet de by-pass et orifice 4 externeRéducteur de pression 3 voies sur A avec clapet de by-pass et orifice 4 externe |
Hauteur d'Empilage | 2,99 in.76 mm |
Plaque porte joints incluse (voir notes) | OuiOui |
Includes integral cartridge(s) | Yes (see Included Components)Yes (see Included Components) |
Cavité | T-22A |
Open Cavities | 11 |
Taille de l'Orifice | 9/16"-18UNF9/16"-18UNF |
In the beginning, the bosses (profiles) were cylindrical and centered on the cavity. The boss created a consistant locating spot for the fixture that put in the bolt through holes. The first step in machining sandwiches was to put in the cavities and this was done using big old #4 Warner-Swazey turret lathes. Adding the circular boss was practically free at this point. When 2 or more sandwiches are stacked they look designed rather than a random stack of blocks. This was deemed esthetically pleasing and became a Sun trademark. You can spot Sun sandwiches from across a factory floor. We switched to CNC in the early 80's but kept the circular boss. At this time the first sandwich with 2 cavities on one side was designed, the YFCG XHN AA. Obviously we could not use a circular boss centered on a cavity; we tried a partial circular boss centered on both of the cavities, but the resulting appearance was poor. The solution was a rectangular boss with radiused corners. The resulting profile was pleasing and more modern looking than the circular boss and served a functional purpose--less material had to be removed. We changed all the other sandwich bosses to match. We have applied the boss profile to some custom manifolds.....just because it looks good.
Il y a exactement 15 gouttes Sun dans un centimètre cube.
- Make sure the surfaces are flat and that there are no burrs. Do not polish the surface; machining marks are good. The machining marks help stop the o-rings from acting as pumps.
- Look for dings on the corners of seal plates that will create gaps.
- Stud rods or cap screws must not bottom out in the sub-plate.
- It is very important to assemble a stack of sandwich valves keeping the o-ring sealing surfaces “dry”. The hydrostatic properties of an oil film under the o-rings, and at the seal plate interface, can create a fluid path leading from the pressurized port interfaces to the outside edge of the stack. (Under this condition, as noted in bullet point 1 above, an o-ring can actually act as a “pump”.) So, if you start with a wet seal interface in your stack, there’s a good chance it will always stay wet!
Reasons to anodize:
- To increase corrosion resistance. Sun uses 6061-T651 aluminum. It is one of the most corrosion resistant aluminum alloys there is. Whether or not anodizing improves the corrosion resistance of 6061 aluminum is debatable. We have yet to have a manifold returned because of corrosion.
- Appearance (color). The 2 colors that would appeal to Sun would be blue or black. Unfortunately these are the colors that are hardest to do consistently.
- To provide a hard wear surface. Sun does not make parts-in-body valves. The manifold is just plumbing. We don't need a wear surface.
- Because everyone else does it. Bad reason.
Reasons to not anodize:
- Cost. It's another process.
- Logistics. When you make tens of thousands of manifolds a month and you anodize hundreds, it's a problem. Consistency. See above.
- Stamping. After a body is anodized you cannot do any more stamping without making a mess.
Inspection. Have you ever tried to look for burrs in a black anodized body? It's the old blackboard factory at night scenario. - Torque. You will experience an increase in breakaway torque when removing items from an anodized manifold.
- Fatigue life. This is the best reason to not anodize. Fatigue failure is a very complex phenomenon. What it takes to initiate a crack is difficult to predict. What it takes to propagate a crack is readily defined. Anodizing produces a very thin, very hard, and very brittle surface on aluminum. The first time you pressurize an anodized aluminum manifold you have initiated fatigue cracks. Whether or not the stress is enough to propagate the cracks is a matter of pressure and manifold geometry. Anodizing an aluminum manifold grossly reduces the fatigue life by anywhere from 20% to 50%.
Yes. If you look in the sandwich section you will see that we offer many such packages. When you are pressurizing B, A is connected to tank, allowing the reducer to do its job. When you reverse, the drain or tank port of the reducer is pressurized by A. This increases the setting of the reducer and helps keep the reducer open in the reverse flow direction.
- La hauteur de l'empilage mentionnée dans le tableau des informations techniques tient compte de la plaque porte-joints.
- Important: Il est indispensable de connaître la pression maximum du système dans lequel le bloc sera intégré. La pression maxi de fonctionnement du bloc dépend de la matière du bloc, alors que le type et la taille des orifices sont secondaires. Par exemple, les blocs fabriqués en aluminium ne sont pas conçus pour des systèmes où la pression est supérieure à 210 bar, quels que soient le type et la taille des orifices.
- Putting Sun at the heart of hydraulic regenerative braking systems
- New Sandwich Bodies
- QuickDesign with SmartConnect Offers Drag-and-Drop Schematic Tool
- Usiner les Cavités pour Cartouches Sun (521.84 Ko)
- Blocs Modulaires (575.9 Ko)
- Recommandations pour les Fluides et les Températures
- QuickDesign & SunDesign: Les Solutions Sun en 3 et 5 Axes
- Sun Model Code Explanation; 999-901-334 (343.9 Ko)
- Blocs Forés: Matières Utilisées dans les Produits SUN
- Custom Integrated Packages from Sun
- Removing Valves from Ductile Manifolds (73.96 Ko)
- LES CARTOUCHES à VISSER SUN à “NEZ FLOTTANT” (447.56 Ko)