Clapet anti-retour, ouverture par pilotage, avec pilote étanche
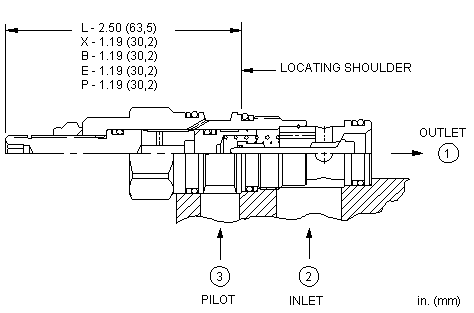
Symbols for CKCD


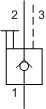
Ce clapet piloté qui s’ouvre quand on le pilote a un piston de pilotage étanche, un siège en acier, et n’est pas drainé. il laisse passer librement le débit depuis le distributeur (chambre 2) vers la charge (chambre 1) et le bloque en sens inverse. Une pression appliquée à l’orifice de pilotage (chambre 3) ouvre la valve de la chambre 1 vers la 2. La pression de pilotage nécessaire dans la chambre 3 pour ouvrir la valve est directement proportionnelle à la pression de charge de la chambre 1. La contre pression sur la chambre 2 s’oppose directement à la pression de pilotage.
- Ces clapets pilotés à l’ouverture à 3 orifices sont physiquement et fonctionnellement interchangeables avec les valves d’équilibrage à 3 orifices (c’est-à-dire le même sens de débit, la même cavité pour une taille donnée). Cependant, les dimensions extérieures de la cartouche peuvent varier.
- Cette valve assure une protection en cas de rupture de flexible. Elle bloque la charge l’empêchant ainsi de dériver.
- Le taux de fuite est extrêmement réduit. Le traitement du clapet et du siège améliorent la durée de vie. Si la charge dérive à cause de la valve, le siège a probablement été endommagé par une pollution et la cartouche doit être remplacée.
- Le piston de pilotage étanche est utilisé pour les circuits où les fuites entre orifices sont indésirables.
- Un orifice de pilotage externe situé sur la partie hexagonale de la cartouche est disponible en option. Dans ce cas, l’orifice 3 est bloqué. Voir options de contrôle E et P.
- Les clapets pilotés à l’ouverture sont destinées à bloquer une charge et non à en contrôler son déplacement. Pour les application de contrôle de charge, utiliser les valves d’équilibrage.
- Pour les modèles équipés de l’option de descente manuelle de la charge, tourner la vis dans le sens horaire pour libérer la charge.
- Les cartouches configurées avec des joints EPDM s’utilisent dans les systèmes avec des fluides ester phosphate. L’exposition de ces joints à des fluides à base de pétrole, de graisse ou de lubrifiant détériorera les joints.
- Les cartouches anticorrosion sont destinées à une utilisation dans les environnements corrosifs et sont identifiées par l'extension /AP quand les parties de la cartouche en contact avec l'air ambiant sont en acier inoxydable, ou l'extension /LH quand les parties de la cartouche en contact avec l'air ambiant sont plaquées Zinc-Nickel. Pour la totalité des options disponibles voir la section CONFIGURATION. Pour plus de détails consulter la fiche "Matières Utilisées dans les Produits SUN" sous l'onglet INFO TECHNIQUES.
- Cette valve intègre le concept Sun de la cartouche à visser "flottante" qui permet de minimiser les contraintes internes dues à un couple de serrage excessif de la cartouche et/ou à des écarts d’usinage des cavités ou des cartouches.
Cavité | T-11A |
Taille | 1 |
Capacité | 15 gpm60 L/min. |
Pression maximale de fonctionnement | 5000 psi350 bar |
Rapport de pilotage | 3/13/1 |
Fuite Maximale à 24 cSt (100 SUS) | 1 drops/min.0,07 cc/min. |
Dimensions du six pans de la valve | 7/8 in.22,2 mm |
Couple de serrage de la valve | 30 à 35 lbf ft41 - 47 Nm |
Poids du composant | 0,20 lb0,10 kg |
Seal kit - Cartridge | Buna: 990011007 |
Seal kit - Cartridge | EPDM: 990011014 |
Seal kit - Cartridge | Polyurethane: 990011002 |
Seal kit - Cartridge | Viton: 990011006 |
Three-port vented pilot-to-open, or atmospherically referenced, check valves are considered problem solvers for existing circuits that used a non-vented valve. If a vented valve is required in a new design, four-port valves are recommended. Atmospherically referenced valves may leak externally and pose a threat for intrusion of moisture (and resulting corrosion) in the spring chamber even though the spring chamber is sealed.
It should be vented immediately downstream of the reason a vented valve is needed. Vented PO checks need the same amount of pilot pressure to open as a non-vented valve but once open they require less than 100 psi of pilot pressure to stay open.
Study the two circuits below.
- In the one on the right, the load is free to move, the check is being held open by normal tank line pressure that is seen as pilot pressure. The circuit on the right may work correctly on start up and then fail when temperatures drop or return line filters get full.
- In the circuit on the left the vent connection nullifies the tank line pressure seen at the pilot connection. The result is zero effective pilot pressure.
Sun's pilot-to-open check valves with a metal-to-metal seat, when new, provide near zero leakage. If the actuator is drifting, and you have determined it is a result of the valve, the metal seat in the valve may have been damaged and it is recommended that a new valve be installed.
Backpressure at the inlet (port 2) directly opposes pilot pressure, effectively increasing the amount of pressure required to open the valve. If the backpressure is flow related (as in a meter-out flow control) the result could be a severe ratcheting movement of the actuator. Using vented load holding valves will prevent this problem.
Pilot-to-open check valves should not be used in paired cylinder circuits. The pilot pressure needed to open a pilot-to-open check is proportional to the load it is holding. The valve with the least load will open first, transferring the combined load to the second valve at more than double the pressure. Use counterbalance valves instead. The pilot pressure to open a counterbalance valve is inversely proportional to the load pressure. When one of the counterbalances opens first the load is transferred to the other counterbalance and lowers the pilot pressure required. The valves cooperate and lower the load with a minimum of load shift.
Generally, pilot-to-open check valves should be mounted as close to the actuator as possible to provide maximum protection in the event of hydraulic hose or line failure. Sun offers many mounting configurations that will accomplish this. Additionally, these cartridges can be installed directly in the actuator by machining a cavity in the actuator housing.
Not exactly. The old style vented check that had the pilot port in the end of the hex body, and vented out port 3, had what we call a proportional pressure reducing feature. The poppet stem was exposed to the vented area and the stem area was about ¼ of the area of the poppet seat. The result was that you could only develop 75% of the pressure at the actuator. If system pressure was 3000 psi (210 bar), the highest pressure at the actuator was about 2250 psi (155 bar). The part numbers for the old style valves are
CKCE CKEE CKGE CKIE CKCF CKEF CKGF CKIF CKCG CKEG CKGG CKIG CKCH CKEH CKGH CKIH
In our 1992 catalog we introduced a new design of vented pilot-to-open check valves, eliminating the proportional pressure reducing feature to allow full system pressure at the actuator. The pilot is now at port 3. This allows the vented counterbalances and the vented checks to share the same manifolds. The new design incorporates more spring force to lessen the chance of false piloting (see the FAQ on where to vent). The new design allows us to offer valves that are vented out of a port in the hex body.
We do have new design valves that replace the old style (pilot in 3 and vent out the hex body). These should be used with caution. If you are replacing the old style that had the pressure reducing feature you will realize a 33% increase in actuator force. The part numbers for these are CKCI, CKEI, CKGI, and CKII.
The venting of the new design is not entirely pure. There is an area exposed to the vent area that opposes the poppet spring. Piloting a valve open is a very remote possibility but 450 psi (30 bar) in the vent area could hold the poppet open.
Good question. We have never published this data. If you compare the area of the pilot piston to the "as manufactured" area of the seat, the ratio of series 0 is a true 3:1, the series 1, 3, and 4 are 4:1 and the series 2 is 4.4:1.
In the beginning, the valve of choice was the Delrin seated valve and because of the compliance of the seat, the ratio went down as the pressure went higher and the poppet sank into the seat. Eventually the seat will take a set and the ratio will also be less at lower pressures. Everything lowers the ratio, even wear and tear on the steel seat. The springs in the valve lower the ratio by a large amount at low operating pressures (see the answer on piloting with air).
The effective pilot ratio is always less than the area ratio. Understating the pilot ratio of our pilot-to-open checks leads to more robust circuits.
Yes, but….. Our valves are meant to work with hydraulic fluids; they are not protected against the water that is in compressed air. Corrosion is a real possibility. Valves that have 30 psi (2 bar) cracking pressures or lower (Z, A, B, and C spring ranges) have 2 springs in them--one to close the poppet and one to return the pilot piston. The spring that returns the pilot piston is worth about 30 to 35 psi (2 to 2,5 bar) of pilot pressure. The minimum pressure to pilot open a CKCB XCN, which is a 30 psi (2 bar) cracking pressure, is about 45 psi (3 bar).
To open a pilot-to-open check valve with 3000 psi (210 bar) at port 1, 1045 psi (72 bar) of pilot pressure is required at port 3; this equates to a 2.9:1 effective pilot ratio. To open a pilot-to-open check valve with 30 psi (2 bar) at port 1, 55 psi (3.8 bar) of pilot pressure is required at port 3; this equates to a 0.5:1 effective pilot ratio.
Direct acting valves are used to prevent over pressure and pilot operated valves are used to regulate pressure. If you are unsure, use a direct acting valve. Sun's direct acting valves are very fast, dirt tolerant, stable, and robust. Sun's pilot operated valves are moderately fast, they have a low pressure rise vs. flow curve, and they are easy to adjust.
Pilot-to-open check valves on the rod side of a cylinder may be a problem because intensification could increase rod side pressure above design limits. Cylinders with large rods may intensify rod end pressure past the point where blind end pressure is enough to pilot the valve open. Use the equations below. For example, the application is a retract-to-clamp cylinder with a blind end area to rod end area ratio of 2:1. Clamping pressure is 2000 psi (140 bar). If the pilot to open check has a pilot ratio of 3:1 it will take more than 2000 psi (140 bar) to pilot the check open and at that point the rod end pressure will have climbed to 6000 psi (420 bar).
Il y a exactement 15 gouttes Sun dans un centimètre cube.
The standard, or bleed through, versions allow a small amount of leakage between port 3 (pilot) and port 2 (inlet), which aids in purging air that can be trapped in the pilot circuit. Versions with sealed pilots may be sluggish to close because of trapped air.
All four-port vented valves have a sealed pilot. On 4-port vented valves, port 4 (vent) should never be blocked as seal weepage will eventually cause the valve to malfunction. 1 to 2 drops of oil pass into the vented spring chamber every 4000 cycles; this equates to 1 cubic inch (16 cc) every 1 million cycles.
There are 4 explanations that we know of:
- Many cycles to high pressures. Back up rings serve a sacrificial purpose. Their job is to fill the clearance gap we need to fit our cartridge into the cavity and protect the primary seal, the O ring. If the gap is too large or the pressure is too high they extrude into the gap and wear away. When a breach in the back up ring occurs the O ring starts to nibble away and fails rather quickly. Under 3000 psi (210 bar) this should never happen. At 5000 psi (350 bar) the seals may need to be replaced after 1,000,000 cycles. Oversized cavities and rough surface finishes can greatly accelerate the wear.
- Incorrectly machined cavities. One common problem is not taking the reamer deep enough to create a good O ring lead. Another is a side connection that violates the O ring lead. The symptom is a slice missing from the seal.
- Undertorqued cartridges. If cartridges are not torqued to a high enough level they may start to back out. When they back out far enough they expose the seals causing abrupt seal failure. The symptom is that there is a section missing from the seal. See the related cartridge back out FAQ.
- Oil filled cavity. The first time the cartridge is pulled is to check a load drift problem. When the cartridge is replaced the drift is worse. Every time the cartridge is checked the seals are displaced. This is an interesting phenomenon that is explainable and demonstrable. It starts with a cavity that is full of oil. Sun load holding cartridges block flow from the nose of the cartridge, port 1, to the side, port 2. When you insert a cartridge into an oil filled cavity, the oil is displaced either into port 2 or outside the manifold. As the nose seals start into their bore they try to seal. If oil cannot be displaced, pressure builds in port 1. As the pressure builds the seals are lifted out of their grooves and shoved up onto the port 2 area. The symptom is the seals are sometimes intact, other times they are severely pinched.
The solution is easy. Stick your finger in the cavity (before you screw in the cartridge). If you create a small air pocket ahead of the cartridge the seals can fully engage their bore before enough pressure builds to displace the seals.
Pilot pressure (port 3) for a pilot-to-open check valve is directly proportional to the load pressure (port 1) . . . the higher the load pressure the more pressure it takes to pilot it open. To calculate the pressure required to release a load, use the following equations
These equations are under ideal conditions and do not consider any backpressure in the circuit.
The pilot ratio is the ratio of the pilot piston area to the check poppet seat area, e.g. in a 3:1 pilot ratio valve, the pilot piston area is 3 times the check poppet seat area.
A pilot-to-open check valve is a load holding valve, not a motion or over-running load control valve. It is not capable of dissipating energy in a controlled fashion. A pilot-to-open check valve is either open or closed; it does not modulate. If you try to use a pilot-to-open check valve to control an over-running load, a severe ratcheting movement of the actuator is likely to occur.
Use a counterbalance valve. In the above example the pressure needed to extend the cylinder would be less than 200 psi.
Our configuration does not lend itself to high ratios. We can't make the pilot piston bigger so the only way would be to make the seat smaller. A smaller seat closes the flow path around the poppet stem and capacity is quickly lost. Besides, we have a solution……use a counterbalance valve.
Because of the very high ratio, the COFO has limited capacity. The discharge path is across a .050 inch (1,3 mm) diameter orifice. If you have large accumulators combined with low precharge pressures, this may not discharge the energy quickly enough. Using the COFO XDN cartridge in conjunction with an LODA XDN will provide capacity for larger applications.
Nothing, they are still available, we just stopped cataloging and promoting them. After years of experience, testing, and engineering we came to the conclusion that they are best suited for moderate pressures, 2000 - 3000 psi (140 - 210 bar). If the seat is soft enough to conform at low pressures, it is too soft to stand up to todays higher operating pressures and flows. If you have a dirty, medium pressure system that does not experience high flows or temperatures and you require very low leakage rates, you may want to consider the soft-seated valves. One piece of hard debris can make a steel seat leak. A soft seat is able to ingest a lot of contamination before it starts to leak. However, one piece of debris can cause the soft seat to leak at low pressures. Originally, Sun had a tighter leakage specification on soft-seated valves. However, when we made the decision to promote the steel seated valves instead of soft seats, we tightened the leakage specifications of the steel seat valves to match.
- CKCDSClapet anti-retour piloté, drain indépendant, pilotage externe en SAE-4, piston pilote étanche
- CKCDVClapet anti-retour piloté, drain indépendant, pilotage externe en 1/4'' NPTF, piston pilote étanche
- Les cartouches de la taille 4 PLUS offrent un débit supérieur pour des pertes de charge inférieures
- Nouvelle Séries Électrovannes & Bobines Sun FLeX ™
- Conseils Techniques pour les Distributeurs Pilotés
- QuickDesign with SmartConnect Offers Drag-and-Drop Schematic Tool
- Cartouches Sun avec joints EPDM
- Conseils Techniques pour les Clapets Anti-Retour, les Valves de Contrôle du Débit et les Régulateurs 3 Voies à Débit Prioritaire
- Sun Étend ses Solutions Anticorrosion
- New FLeX Series Solenoid-Operated Directional Valves
- Conseils Techniques pour les Valves d'Équilibrage et les Clapets Anti-Retour Pilotés
- Nouvel outil de sélection d’équilibrage QuickSelect LoadHolding
- CavitySaver multi-function valves deliver single-cartridge solutions
- Encore Une Solution Optimisée par Sun Hydraulics !
- Nouvelles Électrovalves de Pilotage Sun
- Usiner les Cavités pour Cartouches Sun (521.84 Ko)
- Valves d'Équilibrage et Clapets Anti-Retour Pilotés (870.71 Ko)
- LoadAdaptive™ & LoadMatch™ Cartridges (713.18 Ko)
- Fonctions Spécifiques (462.31 Ko)
- Distributeurs à Pilotage Interne (629.36 Ko)
- Clapets Anti-Retour, Valves de Contrôle du Débit et Régulateurs T (536.99 Ko)
- Performances et Caractéristiques Générales
- LES CARTOUCHES à VISSER SUN à “NEZ FLOTTANT” (447.56 Ko)
- Liste et Définition des Tailles de Cartouche et des Cavités SUN
- Recommandations pour les Fluides et les Températures
- Units of Measure, Settings, and Conversions
- Sun Model Code Explanation; 999-901-334 (343.9 Ko)
- Cartouches: Matières Utilisées dans les Produits SUN