Sensible a la presión regenerador ensamblaje
Function
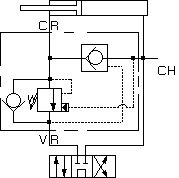
Modifiers | Ports |
D, D/S | Ports CH, CR, VR: 3/4" NPTF; Mounting Holes: .375 - 16UNC x .62 DP; |
E, E/S | Ports CH, CR, VR: 1" NPTF; Mounting Holes: .375 - 16UNC x .62 DP; |
F, F/S | Ports CH, CR, VR: 1 1/4" NPTF; Mounting Holes: .375 - 16UNC x .62 DP; |
L, L/S | Ports CH, CR, VR: SAE 12; Mounting Holes: .375 - 16UNC x .62 DP; |
M, M/S | Ports CH, CR, VR: SAE 16; Mounting Holes: .375 - 16UNC x .62 DP; |
N, N/S | Ports CH, CR, VR: SAE 20; Mounting Holes: .375 - 16UNC x .62 DP; |
P, P/S | Ports CH, CR, VR: 1" Code 61; Mounting Holes: .375 - 16UNC x .62 DP; |
P/M, P/T | Ports CH, CR, VR: 1" Code 61; Mounting Holes: M10 x 1.5-6H x .62 DP; |
W, W/S | Ports CH, CR, VR: 3/4" BSPP; Mounting Holes: M10 x 1.5-6H x .62 DP; |
X, X/S | Ports CH, CR, VR: 1" BSPP; Mounting Holes: M10 x 1.5-6H x .62 DP; |
Y, Y/S | Ports CH, CR, VR: 1 1/4" BSPP; Mounting Holes: M10 x 1.5-6H x .62 DP; |
The pressure sensitive regenerative valve assembly allows a double-acting, single rod cylinder to be extended more rapidly using the same pump flow. To achieve this, oil from the rod end of the cylinder (CR) is added to the pump flow to the blind end (CH), increasing the rate of extension. It incorporates a pressure adjustable, counterbalance valve that provides a smooth transition when the load is engaged and pressure in the blind end rises to approximately 25% of the set point of the counterbalance valve, at which time the regenerative flow decreases smoothly until rod end flow is fully diverted to tank (VR). Full pump pressure is then applied to the blind end area developing maximum force.
- Capacity refers to pump flow or regeneration flow, which is the flow coming out of the rod side of the cylinder, whichever is larger
- This valve assembly will not prevent a load from extending the cylinder. The best way to prevent this is to use a vented counterbalance valve mounted directly to the rod end of the cylinder. A non-vented valve will not work.
- The ideal cylinder ratio to use with regeneration is 2:1, the blind end area being twice what the annular area at the rod end. A 2:1 cylinder in regen gives the same speed extending as retracting.
- Cylinders with ratios above 2:1 (large rods) will function correctly but with less speed gain. Intensification needs to be considered with higher ratios. A 2:1 cylinder may generate a pressure on the rod side that is twice system pressure unless steps are taken to limit it.
- Cylinders with ratios as low as 1.5:1 (small rods) may work if care is used in designing the application. As the rod diameter gets smaller in relation to the piston diameter the flows increase dramatically and the force available drops accordingly.
- Cylinders with ratios below 1.5:1 are unlikely to result in a working regenerative application because of the small area of the rod and the high flows that would be generated.
- When a cylinder is in the regenerative mode the only force available is the pressure working on the rod area.
- The counterbalance valve in this assembly is not acting as a counterbalance valve; it is acting as a pressure sensitive unloading valve. The setting, however, relates to the counterbalance world. With the CB*A set at 4000 psi (280 bar), the circuit will start to come out of regen with about 1000 psi (70 bar) of blind end pressure and will then start to gain force somewhere above 1400 psi (90 bar).
- Regeneration is only possible in the extend direction.
Body Type | montaje en líneamontaje en línea |
Capacity | 50 gpm200 L/min. |
Mounting Hole Quantity | 22 |
There are exactly 250 Sun drops in a cubic inch or 15 in a cc.
Reasons to anodize:
- To increase corrosion resistance. Sun uses 6061-T651 aluminum. It is one of the most corrosion resistant aluminum alloys there is. Whether or not anodizing improves the corrosion resistance of 6061 aluminum is debatable. We have yet to have a manifold returned because of corrosion.
- Appearance (color). The 2 colors that would appeal to Sun would be blue or black. Unfortunately these are the colors that are hardest to do consistently.
- To provide a hard wear surface. Sun does not make parts-in-body valves. The manifold is just plumbing. We don't need a wear surface.
- Because everyone else does it. Bad reason.
Reasons to not anodize:
- Cost. It's another process.
- Logistics. When you make tens of thousands of manifolds a month and you anodize hundreds, it's a problem. Consistency. See above.
- Stamping. After a body is anodized you cannot do any more stamping without making a mess.
Inspection. Have you ever tried to look for burrs in a black anodized body? It's the old blackboard factory at night scenario. - Torque. You will experience an increase in breakaway torque when removing items from an anodized manifold.
- Fatigue life. This is the best reason to not anodize. Fatigue failure is a very complex phenomenon. What it takes to initiate a crack is difficult to predict. What it takes to propagate a crack is readily defined. Anodizing produces a very thin, very hard, and very brittle surface on aluminum. The first time you pressurize an anodized aluminum manifold you have initiated fatigue cracks. Whether or not the stress is enough to propagate the cracks is a matter of pressure and manifold geometry. Anodizing an aluminum manifold grossly reduces the fatigue life by anywhere from 20% to 50%.
Direct-acting valves are used to prevent over pressure, and pilot-operated valves are used to regulate pressure. If you are unsure, use a direct-acting valve. Sun's direct acting valves are very fast, dirt tolerant, stable, and robust. Sun's pilot-operated valves are moderately fast, they have a low pressure rise vs. flow curve, and they are easy to adjust.
- Important: Carefully consider the maximum system pressure. The pressure rating of the manifold is dependent on the manifold material, with the port type/size a secondary consideration. Manifolds constructed of aluminum are not rated for pressures higher than 3000 psi (210 bar), regardless of the port type/size specified.
- For detailed information regarding the cartridges contained in this assembly, click on the models codes shown in the Included Components tab.
- CONJUNTOS DE VÁLVULAS DE REGENERACIÓN SUN
- NUEVO: Soluciones de control de flujo con prioridad ajustable
- Conjuntos integrados: Soluciones que hacen crecer su reputación
- Nuevas soluciones rápidas de avance y alimentación
- Putting Sun at the heart of hydraulic regenerative braking systems
- Manufacturing Sun Cartridge Cavities (522.27 KB)
- Sun's Floating Style Screw-In Cartridge (1.06 MB)
- Fluid Recommendations: Oil Viscosity, Cleanliness & Temperature
- Sun Model Code Explanation; 999-901-334 (343.9 KB)
- Custom Integrated Packages from Sun