3:1 pilot ratio, standard capacity counterbalance valve assembly
Symbols
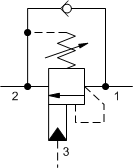
Port Headings and Sizes [ + ]
Modifiers | Ports |
EBA, /10, /11, /15, /16, /S, /S3, /V, /Y, /Y3 | Gage Port (Plugged): 1/4" NPTF; |
EBA/1A, /1B, /1F, /1G, /M, /T, /T3, /W, /W3, /Z | Gage Port (Plugged): 1/4" BSPP; |
Cartridge Technical Features [ + ]
Counterbalance valves with pilot assist are meant to control an overrunning load. The check valve allows free flow from the directional valve (port 2) to the load (port 1) while a direct-acting, pilot-assisted relief valve controls flow from port 1 to port 2. Pilot assist at port 3 lowers the effective setting of the relief valve at a rate determined by the pilot ratio.
Other names for this valve include motion control valve and over-center valve.
- Counterbalance valves should be set at least 1.3 times the maximum load induced pressure.
- Turn adjustment clockwise to decrease setting and release load.
- Full clockwise setting is less than 200 psi (14 bar).
- Backpressure at port 2 adds to the effective relief setting at a ratio of 1 plus the pilot ratio times the backpressure.
- Reseat exceeds 85% of set pressure when the valve is standard set. Settings lower than the standard set pressure may result in lower reseat percentages.
- Sun counterbalance cartridges can be installed directly into a cavity machined in an actuator housing for added protection and improved stiffness in the circuit.
- Two check valve cracking pressures are available. Use the 25 psi (1,7 bar) check unless actuator cavitation is a concern.
- All 3-port counterbalance, load control, and pilot-to-open check cartridges are physically interchangeable (i.e. same flow path, same cavity for a given frame size).
- This valve does not have positive seals on the pilot section and will pass up to 3 in³/min.@1000 psi (45 ml/min.@70 bar ) between port 2 and port 3. This is a consideration in master-slave circuits and in the leak testing of valve-cylinder assemblies.
- Cartridges configured with EPDM seals are for use in systems with phosphate ester fluids. Exposure to petroleum based fluids, greases and lubricants will damage the seals.
- Corrosion-resistant cartridge valves are intended for use in corrosive environments and are identified by the model code suffix /AP for external stainless steel components, or /LH for external zinc-nickel plated components. See the CONFIGURATION section for all options. For further details, please see the Materials of Construction page located under TECH RESOURCES.
- Incorporates the Sun floating style construction to minimize the possibility of internal parts binding due to excessive installation torque and/or cavity/cartridge machining variations.
Cartridge Technical Data [ + ]
Note: Data may vary by configuration. See CONFIGURATION section.
Cavity | T-11A |
Series | 1 |
Capacity | 15 gpm60 L/min. |
Pilot Ratio | 3:13:1 |
Maximum Recommended Load Pressure at Maximum Setting | 3075 psi215 bar |
Maximum Setting | 4000 psi280 bar |
Pilot Configuration | Bleed throughBleed through |
Factory Pressure Settings Established at | 2 in³/min.30 cc/min. |
Maximum Valve Leakage at Reseat | 5 drops/min.0,3 cc/min. |
Adjustment - No. of CCW Turns from Min. to Max. Setting | 3.753.75 |
Operating Characteristic | StandardStandard |
Reseat | >85% of setting>85% of setting |
Valve Hex Size | 7/8 in.22,2 mm |
Valve Installation Torque | 30 - 35 lbf ft41 - 47 Nm |
Adjustment Screw Internal Hex Size | 5/32 in.4 mm |
Locknut Hex Size | 9/16 in.15 mm |
Locknut Torque | 80 - 90 lbf in.9 - 10 Nm |
Model Weight | .40 lb0,20 kg |
Seal kit - Cartridge | Buna: 990011007 |
Seal kit - Cartridge | EPDM: 990011014 |
Seal kit - Cartridge | Polyurethane: 990011002 |
Seal kit - Cartridge | Viton: 990011006 |
Manifold Technical Data [ + ]
Body Type | SandwichSandwich |
Interface | ISO 03ISO 03 |
Body Features | On A or B, port 3 to opposite sideOn A or B, port 3 to opposite side |
Stack Height | 1.75 in.44,5 mm |
Seal Plate Included (see notes) | YesYes |
Open Cavities | 11 |
Cavity | T-11A |
Port Size | 1/4" NPTF1/4" NPTF |
CAD Files [ + ]
Symbol File Formats
Click the link of the file format you want to download.
CAD File Formats
Click the link of the file format you want to download.
Notes [ + ]
- Stack height value in technical data table includes seal retainer plate.
- Customer to install locating pin according to functional orientation required.
- Important: Carefully consider the maximum system pressure. The pressure rating of the manifold is dependent on the manifold material, with the port type/size a secondary consideration. Manifolds constructed of aluminum are not rated for pressures higher than 3000 psi (210 bar), regardless of the port type/size specified.
Additional Resources [ + ]
Highlights
- Sun's New FLeX Series Solenoid Valves & Coils
- Sun Sandwich Bodies Interchangeable with Bosch and Others
- Pursuing the Perfect Counterbalance Valve
- Counterbalance/Pilot-to-Open Cartridge Valve Technical Tips
- QuickDesign with SmartConnect Offers Drag-and-Drop Schematic Tool
- Sun Offers Zinc-Nickel Plating for Corrosion Resistance
- New QuickSelect LoadHolding Selector Tool
- Sun Expands Corrosion-Resistant Solutions
- Sun LoadMatch™ Valves Save Energy!
- Putting Sun at the heart of hydraulic regenerative braking systems
- Sun Saves Energy with LoadMatch™ Technology
- Sun Cartridges with EPDM Seals
Technical Tips
- LoadAdaptive™ & LoadMatch™ Cartridges (713.18 KB)
- Manufacturing Sun Cartridge Cavities (522.27 KB)
- Counterbalance and Pilot-to-Open Check Valves (1.19 MB)
- Choosing Counterbalance Valves
- Mounting and Assembly of Sandwich Bodies (575.9 KB)
Technical Information
- Performance Data
- Sun's Floating Style Screw-In Cartridge (1.06 MB)
- A Guide to Sun's Counterbalance Families
- Cavity Information (S-171) and Tooling
- Sun Model Code Explanation; 999-901-334 (343.9 KB)
- Cartridges: Materials of Construction
- Custom Integrated Packages from Sun
- Fluid Recommendations: Oil Viscosity, Cleanliness & Temperature
- Manifolds: Materials of Construction
- QuickDesign & SunDesign: Sun's 3- & 5-Axis Solutions
- Units of Measure, Settings, and Conversions
- Removing Valves from Ductile Manifolds (73.96 KB)
- Counterbalance Quick Reference (93.57 KB)